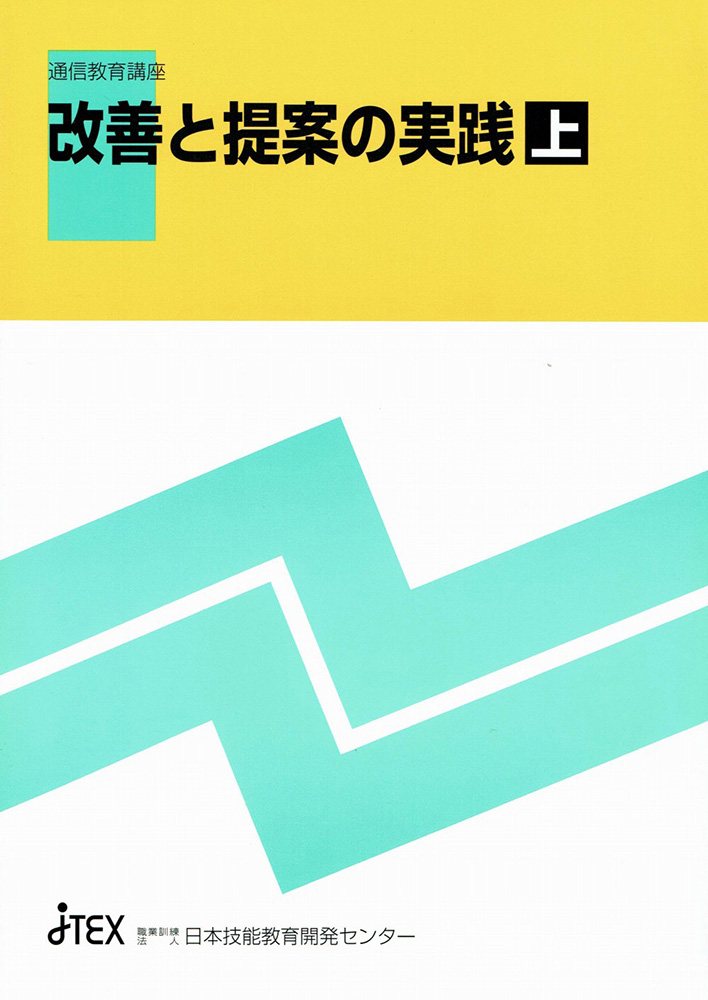
改善と提案の実践
一般受講料:23,100円
特別受講料:20,900円
講座コードI30
受講期間4ヶ月
難易度中級レベル
【目標】 現場での作業改善を立案し、それを実践する能力を身につける!
製造工程の入口から出口まであらゆる場面の改善法を習得!
製造現場は「よいものを、早く、安く、安全に、製品として完成する」という使命を担っています。したがって、多くの企業では早くから「改善提案制度」や、「小集団活動」などを導入して、品質や能率および安全を主眼とした改善活動を活発に展開してきました。
しかし、一方では改善活動のマンネリ化に起因する停滞や形式的活動に対する消極的な取組みなど、必ずしも効果的な改善活動の運営にいたっていません。その原因を分析してみると、作業改善そのものに対する理解不足、改善意識の欠如、改善手法の未熟など、第一線監督者と作業者である私たちにも問題があるようです。
本講座は、この視点を重視した実際に役立つ「改善提案」をねらった構成です。教材のとりあげ方も、受講者に語りかけるよう工夫しました。
学習目標
- 作業改善の立案テクニック、それを実践する改善技法、そしてこれからの改善技法までを習得します。
- 現場での作業改善が立案でき、それを実践する能力が身につきます。
改善と提案の実践の関連講座
教材構成
使用教材
- テキスト2冊(上・下)
- レポート(提出回数4回)
著者
- 青山 正大(青木技術経営事務所)
カリキュラム
No. | 主な項目 |
---|---|
1 |
第1章 作業改善の重要性
第2章 作業改善の歴史
第3章 作業改善の着眼点
|
2 |
第4章 品質の改善
第5章 コストの改善
第6章 作業方法の改善
|
3 |
第7章 安全性の改善
第8章 設備・機械の改善
第9章 5Sのすすめ方
|
4 |
第10章 職場ぐるみの改善活動
第11章 改善提案のすすめ方
第12章 新時代の展望と対応
|