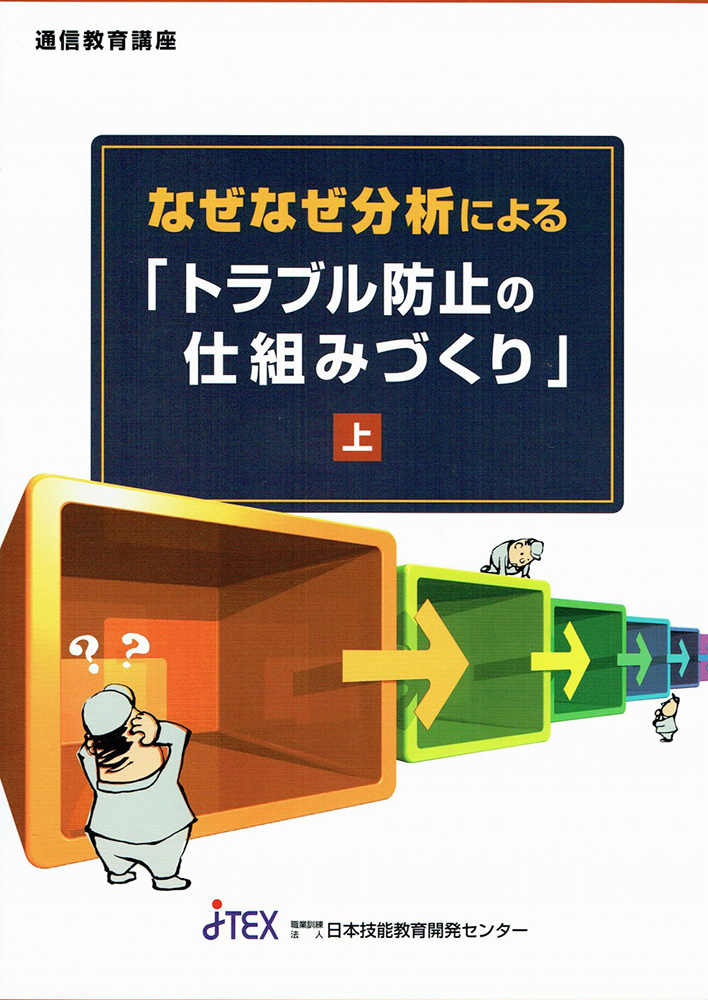
なぜなぜ分析による「トラブル防止の仕組みづくり」
特別受講料:19,800円
一般受講料:22,000円
講座コードH24
受講期間3ヶ月
難易度中級 上級レベル
ねらい
不良品発生の真因に手を打ち、トラブル発生・再発の防止を!
「なぜなぜ分析」とは、現象を発生させている要因を理論的に分析する方法です。
「人、機械・設備、材料・部品、方法、測定、環境、情報」(5M1EI)などの変化を事前に察知し、未然防止対策を行うための管理を「変更管理」といいます。
本講座では、「なぜなぜ分析」「変更管理」「改善活動の進め方」について、具体的な事例を、図解や書式を用いて説明します。これらの理解により、トラブル防止の仕組みづくりについて、効果をあげていくことをねらいとします。
講座の特色
- 「なぜなぜ分析」の手法を、改善活動の活性化、成果の向上に結びつけます。
- 改善活動の進め方(問題解決型、課題達成型、施策実行型)を理解し、実践することができます。
教材構成
- テキスト2冊
- レポート回数:3回
主な項目
No. | 主な項目 |
---|---|
1 |
序章 「なぜなぜ分析」の学習をはじめるにあたって第1章 問題とは、課題とは
第2章 「なぜなぜ分析」とは
第3章 「なぜなぜ分析」手法の活用
第4章 個人演習
|
2 |
第5章 「変更管理」とは
第6章 品質保証の仕組みづくり
第7章 参考資料
第8章 「なぜなぜ分析と変更管理」のQ&A
第9章 工程変更マニュアル
第10章 工程変更管理レベルと手続き
|
3 |
第11章 日常での工程変更管理
第12章 変更管理に有効な管理手法
第13章 管理と改善、改善活動の各手順の比較
第14章 問題解決の進め方・まとめ方のポイント
第15章 課題達成の進め方・まとめ方のポイント
第16章 施策実行の進め方・まとめ方のポイント
|
受講者の声
テキスト内容が簡略化されて理解が難しく質問しなければならない構成だった。質問券の回答は明確で分かりやすかった。課題問題はテキストの丸暗記で解けるものでした。
会社で同内容の取組みをしているが、その理解と考え方の補強ができて良かった。なぜなぜ分析のコツと実例があればと感じました。
自部署で今後取り組むべき内容が満載でした。郵便後納等の方法で切手を調達しなくても済むようにしてもらいたいと毎回言っている。
「やるべきこと」の他に「これは控えたほうがよい」や「やってはいけない」などの禁止事項も載っており、勉強になりました。
「変更管理」という言葉は使ったことがなかったのですが、今回学んだことを参考に今後の業務に活用しようと思います。