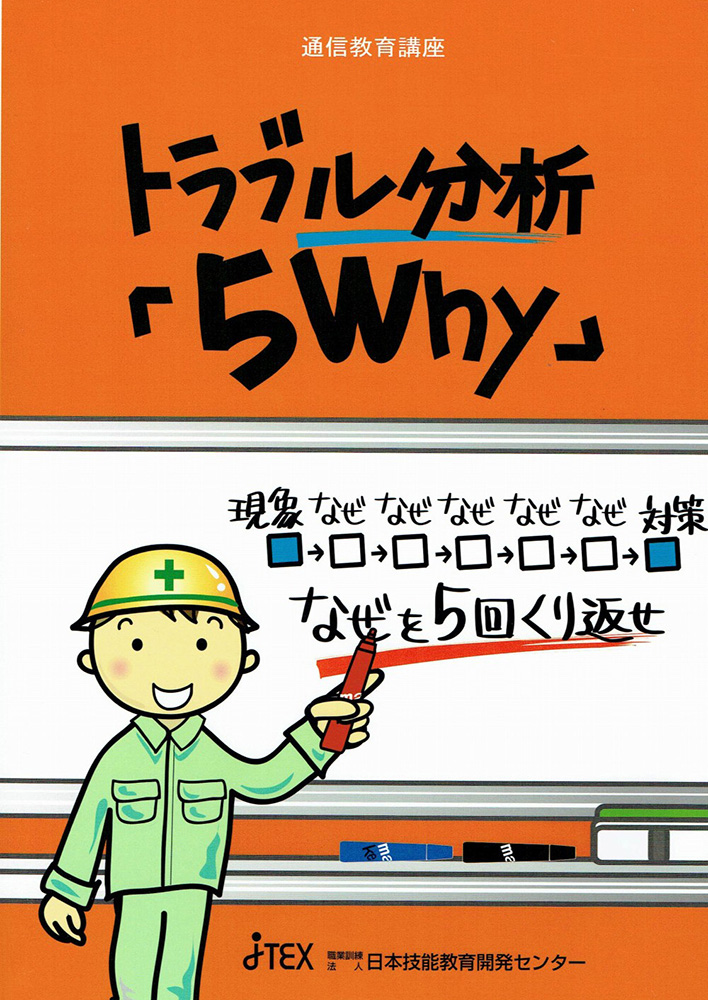
トラブル分析「5 WHY」
特別受講料:15,400円
一般受講料:17,600円
講座コードH17
受講期間2ヶ月
難易度入門 初級レベル
ねらい
「問題の真因」を見付け出す手法を学び、各業務への展開を学ぶ!
各企業では収益を確保するため従来にも増して、現場に根ざした「改善活動」が求められています。
「トラブル分析「5 Why」」手法は、現場・現実を直視して問題発生の仕組みをはっきりと把握し、「問題の真因」を見つけ出し、改善へとつなげていく重要なツールです。
本講座では「トラブル分析「5 Why」」手法の活用法を各種の事例を通してマスターし、職場での安全衛生・品質・保全の向上への展開を学習していきます。
講座の特色
- 「5 Why」手法を学びます。
- 「5 Why」手法のルール、導入の手順を学びます。
- 安全衛生・品質管理・設備保全への「5 Why」手法の導入のしかたがわかるようになります。
教材構成
- テキスト1冊
- レポート回数:2回
主な項目
No. | 主な項目 |
---|---|
1 |
第1章 「5 Why」手法の基本事項
第2章 「5 Why」手法を用いた安全衛生の向上
|
2 |
第3章 「5 Why」手法を用いた品質管理の向上
第4章 「5 Why」手法を用いた設備保全の向上
|
受講者の声
過去に学んだことの再履修ができ基礎が固められた。(なぜなぜ分析、QC手法、TPM活動etc)。図解が適度に挿入されて分かり易かった。
仕事の進め方や改善などを見直すことができ、自分で考える能力を得たと思います。
不具合が発生した時の考え方や、処理対策を立てる時の基本が理解できました。
品質に関する5Whyだけでなく、安全衛生や保全の5Whyについても認識できたことは良かったと思います。
仕事において「なぜなぜ分析」を使う場面があって、その時はよく内容がわかりませんでした。今回の勉強により、理解することができて良かったです。